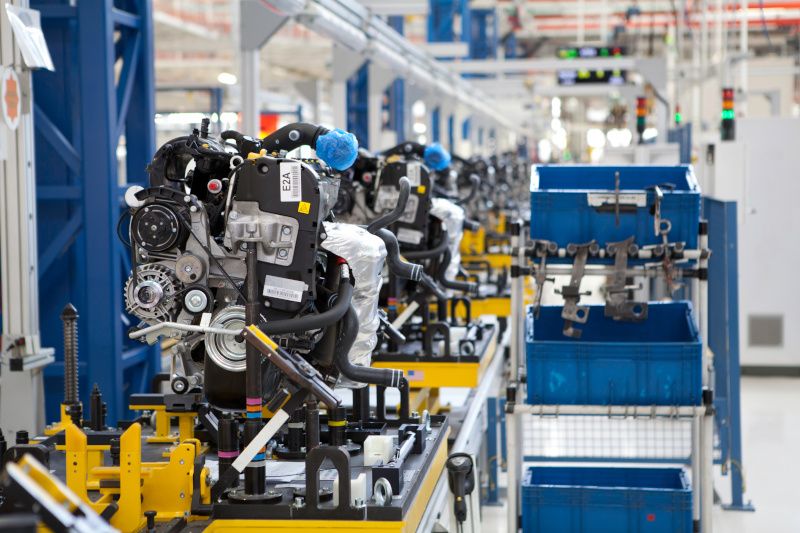
LEAN Consulting
Für viele Unternehmen stellt der Begriff LEAN nicht mehr dar, als ein veraltetes Managementtool der 2000er Jahre. Für die meisten aber sind die Konzepte der schlanken Fabrik heute die Basis ihres operativen Erfolges – und so sehen es auch wir. Auch im Zeitalter von Digitalisierung und künstlicher Intelligenz. Mit mehr als 30 Jahren Erfahrung im LEAN-Consulting unterstützen wir HANDS-ON Unternehmen auf Ihrem Weg zur Weltklasse in der Produktion (Lean Manufacturing) oder im indirekten Bereich (LEAN Office).

Interesse am Thema LEAN? An Branchen- und Umsetzungsbeispielen? Kontaktieren Sie mich einfach, ich helfe gerne telefonisch oder via Email weiter.
Walter Meitz
+43 664 654 06 79
This email address is being protected from spambots. You need JavaScript enabled to view it.
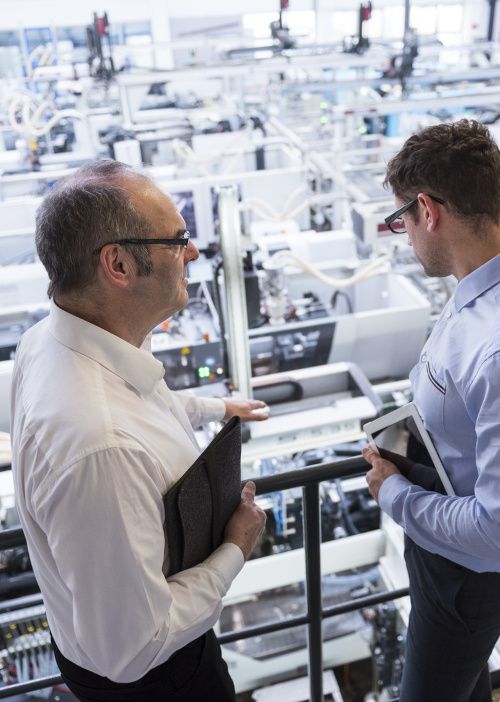
Umsetzungsorientierte LEAN Beratung
Umsetzungsorientierte Beratung stellt einen essenziellen Ansatz dar, um Unternehmen und Organisationen bei der erfolgreichen Umsetzung von Veränderungen, Projekten und strategischen Zielen zu unterstützen. Diese Form der Beratung fokussiert sich nicht nur auf theoretische Konzepte, sondern legt den Schwerpunkt auf die praktische Realisierung von Vorhaben.Umsetzungsorientierte Beratung zeichnet sich dadurch aus, dass sie über die bloße Entwicklung von Ideen und Strategien hinausgeht. Ihr Hauptziel ist es, die praktische Umsetzung von Veränderungen zu begleiten und sicherzustellen, dass die geplanten Maßnahmen erfolgreich in die Tat umgesetzt werden. Dieser Ansatz erfordert eine enge Zusammenarbeit zwischen Beratern und den Mitarbeitern auf allen Ebenen einer Organisation.
Vorteile der Umsetzungsorientierung
- Praktische Lösungen: Statt abstrakter Theorien werden konkrete Lösungen entwickelt, die den spezifischen Bedürfnissen und Herausforderungen eines Unternehmens entsprechen.
- Schnellere Ergebnisse: Die Fokussierung auf die Umsetzung führt zu schnelleren Ergebnissen und sorgt dafür, dass Veränderungen effizienter durchgeführt werden.
- Engagement der Mitarbeiter: Durch die Einbindung der Mitarbeiter in den Umsetzungsprozess entsteht ein höheres Engagement und eine stärkere Identifikation mit den Veränderungen.
- Messbarer Erfolg: Umsetzungsorientierte Beratung legt Wert auf messbare Ergebnisse und Erfolgskontrolle, was eine kontinuierliche Verbesserung ermöglicht.
- Nachhaltigkeit: Die erarbeiteten Lösungen sind oft nachhaltiger, da sie von den Mitarbeitern aktiv mitgestaltet und übernommen werden.
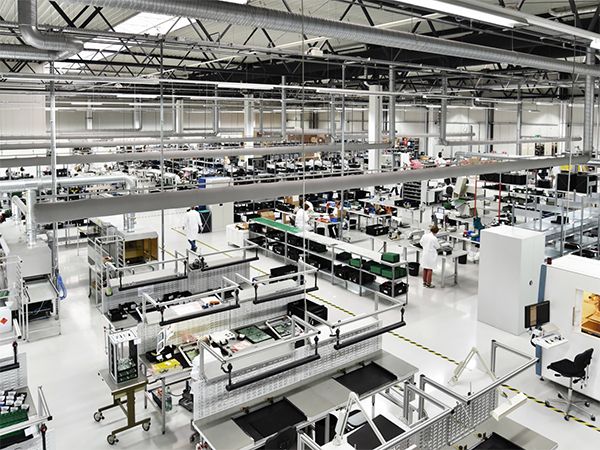
LEAN PRODUCTION
In der heutigen Wirtschaftswelt, in der Effizienz und Wettbewerbsfähigkeit von zentraler Bedeutung sind, hat sich die konsequente Umsetzung der LEAN Production Philosophie als unverzichtbarer Ansatz für auf Weltklasseniveau agierende Unternehmen etabliert.
LEAN Production ist ein kraftvoller Ansatz, der Unternehmen dabei unterstützt, ihre Produktionsprozesse zu optimieren, Verschwendung zu reduzieren und eine nachhaltige Effizienzsteigerung zu erreichen. Durch die Anwendung der LEAN-Prinzipien können Unternehmen nicht nur Kosten senken, sondern auch ihre Wettbewerbsfähigkeit stärken und eine höhere Produktqualität gewährleisten. In einer sich ständig verändernden Geschäftswelt ist LEAN Production ein bewährter Weg, um zukunftsorientiert und erfolgreich zu agieren.
Lean Production Beratung und Training aus einer Hand
In einer zunehmend wettbewerbsorientierten Wirtschaft ist die Optimierung von Produktionsprozessen unerlässlich. Unser Beratungsangebot im Bereich Lean Production unterstützt Unternehmen dabei, Verschwendung zu reduzieren, Prozesse zu verschlanken und nachhaltig mehr Wert zu schaffen. Doch wir gehen einen Schritt weiter: Neben der strategischen Beratung bieten wir ein umfassendes Trainingsangebot, das Ihre Mitarbeitenden befähigt, die Prinzipien von Lean Production effektiv umzusetzen.
Beratung: Maßgeschneiderte Lean-Strategien für Ihr Unternehmen
Unser Ansatz beginnt mit einer präzisen Analyse Ihrer bestehenden Prozesse. Gemeinsam identifizieren wir Optimierungspotenziale und entwickeln eine individuelle Roadmap, die sich an den spezifischen Anforderungen Ihres Unternehmens orientiert. Ob Einführung von Kanban, Just-in-Time-Prinzipien oder die Implementierung von 5S – wir begleiten Sie von der Konzeption bis zur Umsetzung.
Training: Lean-Kompetenz auf allen Ebenen
Nachhaltiger Erfolg entsteht, wenn alle Mitarbeitenden die Lean-Philosophie verinnerlichen. Daher bieten wir praxisorientierte Schulungen für unterschiedliche Zielgruppen an – vom Shopfloor-Mitarbeiter bis zur Führungsebene. Unsere Trainings umfassen:
- Grundlagen von Lean Production: Einführung in die Prinzipien und Werkzeuge
- Kaizen-Workshops: Kontinuierliche Verbesserung erlebbar machen
- Value Stream Mapping: Optimierung der Wertschöpfungskette
- Führungskräftetraining: Lean-Leadership für nachhaltige Kulturveränderung
Ihr Mehrwert
Durch die Kombination von Beratung und Training erhalten Sie nicht nur optimierte Prozesse, sondern auch ein Team, das diese kontinuierlich weiterentwickelt. Unsere Expertise basiert auf mehr als 200 erfolgreich umgesetzten Projekten – von mittelständischen Unternehmen bis hin zu globalen Konzernen.
Setzen Sie auf Effizienz und Expertise. Kontaktieren Sie uns noch heute, um Ihre Lean Production Strategie gemeinsam mit uns zu starten.
LEAN Prinzipien
Wertorientierung ist das Fundament von Lean Production und stellt den Kunden in den Mittelpunkt aller Unternehmensaktivitäten. Das Konzept beginnt mit der grundlegenden Frage: Was genau schätzt der Kunde am Produkt oder an der Dienstleistung? In diesem Zusammenhang ist „Wert“ als etwas zu verstehen, das der Kunde bereit ist, zu bezahlen, weil es seine Bedürfnisse erfüllt oder seine Probleme löst. Unternehmen müssen tief in die Kundenperspektive eintauchen, um diese Bedürfnisse genau zu verstehen und zu definieren, welche Aspekte des Produkts oder der Dienstleistung tatsächlich Mehrwert schaffen.
Ein Unternehmen, das Wertorientierung ernst nimmt, stellt sicher, dass jeder Schritt im Produktionsprozess direkt auf die Schaffung dieses Wertes abzielt. Dazu gehört, dass nicht-wertschöpfende Tätigkeiten, die keinen direkten Nutzen für den Kunden bieten, minimiert oder vollständig eliminiert werden. Diese Aktivitäten werden oft als Verschwendung angesehen und können in Kategorien wie Überproduktion, Wartezeiten, unnötige Transporte, überschüssige Bestände, übermäßige Verarbeitung, unnötige Bewegungen und Fehler eingeteilt werden. Indem Unternehmen sich strikt auf die Schaffung von Wert konzentrieren, können sie ihre Ressourcen gezielter einsetzen, die Kundenzufriedenheit steigern und letztlich ihre Wettbewerbsfähigkeit erhöhen.
Die Wertstromanalyse ist ein strategisches Werkzeug in Lean Production, das Unternehmen hilft, den gesamten Produktionsprozess zu durchleuchten und zu verstehen, wie Wert fließt – vom Rohmaterialeingang bis hin zur Auslieferung des Endprodukts an den Kunden. Ziel dieser Analyse ist es, jeden einzelnen Schritt im Prozess zu kartieren und zu bewerten, um die tatsächlichen Wertströme und auch die auftretenden Ineffizienzen sichtbar zu machen.
Dieser Prozess beginnt typischerweise mit der Erstellung einer Wertstromkarte, die alle Aktivitäten im Produktionsablauf abbildet, sowohl die wertschöpfenden als auch die nicht-wertschöpfenden. Durch die visuelle Darstellung des Wertstroms können Unternehmen Engpässe, unnötige Wartezeiten, überflüssige Arbeitsschritte und andere Formen der Verschwendung leicht identifizieren. Auf dieser Grundlage können sie dann gezielt Maßnahmen ergreifen, um die Effizienz zu steigern, die Durchlaufzeiten zu verkürzen und den Fluss der Produktion zu verbessern. Die Wertstromanalyse ist nicht nur ein Werkzeug zur Problemerkennung, sondern auch ein wesentlicher Schritt, um strategische Verbesserungen und Optimierungen im gesamten Produktionsprozess zu planen und umzusetzen.
Das Fluss-Prinzip ist eine zentrale Säule der Lean Production und strebt danach, den Produktionsprozess so zu gestalten, dass Materialien und Informationen kontinuierlich und ohne Unterbrechungen durch die Wertschöpfungskette fließen. Dieses Prinzip basiert auf der Erkenntnis, dass Unterbrechungen im Produktionsfluss – sei es durch Engpässe, Wartezeiten oder ineffiziente Arbeitsabläufe – zu erheblichen Verschwendungen führen und die Gesamteffizienz der Produktion mindern können.
Ein optimierter Fluss bedeutet, dass jeder Produktionsschritt nahtlos in den nächsten übergeht, ohne dass Materialien zwischengelagert werden müssen oder Ressourcen ungenutzt bleiben. Dies erfordert eine sorgfältige Planung und Synchronisierung der Produktionsprozesse, um sicherzustellen, dass alle Ressourcen – Maschinen, Materialien, Arbeitskräfte – stets verfügbar sind und optimal genutzt werden. Ein kontinuierlicher Fluss reduziert die Produktionszeit und minimiert die Kosten, da weniger Ressourcen für das Management von Zwischenbeständen und Wartezeiten benötigt werden. Darüber hinaus trägt ein flüssiger Produktionsablauf dazu bei, die Flexibilität des Unternehmens zu erhöhen, sodass es schneller auf Veränderungen in der Nachfrage reagieren kann.
Das Pull-Prinzip ist ein weiteres zentrales Konzept in der Lean Production, das darauf abzielt, Produktion und Lagerhaltung streng an der tatsächlichen Nachfrage zu orientieren. Anstatt Produkte auf Verdacht und basierend auf Prognosen in großen Mengen auf Lager zu produzieren (wie es beim Push-Prinzip der Fall ist), werden beim Pull-Prinzip Produkte erst dann gefertigt, wenn eine konkrete Nachfrage besteht. Dies stellt sicher, dass nur das produziert wird, was der Kunde wirklich benötigt, und verhindert somit Überproduktion und die damit verbundenen hohen Lagerkosten.
Das Pull-Prinzip erfordert eine enge Abstimmung und Kommunikation entlang der gesamten Lieferkette, um sicherzustellen, dass die notwendigen Materialien und Komponenten genau dann verfügbar sind, wenn sie gebraucht werden. Dies reduziert nicht nur den Lagerbedarf, sondern auch das Risiko, auf unverkauften Produkten sitzen zu bleiben, die möglicherweise veralten oder nicht mehr den aktuellen Kundenanforderungen entsprechen. Darüber hinaus ermöglicht das Pull-Prinzip eine höhere Flexibilität und Reaktionsfähigkeit, da Unternehmen in der Lage sind, ihre Produktion schnell an Veränderungen in der Nachfrage anzupassen, ohne dabei hohe Vorlaufkosten zu riskieren. Es fördert eine effizientere Nutzung der Ressourcen und unterstützt die Just-in-Time-Produktion, bei der Materialien und Teile genau zum richtigen Zeitpunkt bereitgestellt werden, um den Produktionsprozess zu unterstützen.
Die kontinuierliche Verbesserung, bekannt als Kaizen, ist das Herzstück der Lean Production und verkörpert eine Philosophie, die auf ständiger, schrittweiser Verbesserung basiert. Kaizen ist mehr als nur ein Prozess; es ist eine Haltung und eine Unternehmenskultur, die darauf abzielt, jeden Aspekt der Produktion und des Geschäftsablaufs zu optimieren. Dieser Ansatz betont, dass es nicht unbedingt die großen, radikalen Veränderungen sind, die den größten Unterschied machen, sondern die Summe vieler kleiner Verbesserungen, die kontinuierlich und beständig über die Zeit hinweg umgesetzt werden.
Kaizen ermutigt jeden Mitarbeiter im Unternehmen, unabhängig von seiner Position, aktiv nach Möglichkeiten zur Verbesserung der Arbeitsabläufe, Prozesse, Qualität und Effizienz zu suchen. Durch die Einbindung aller Mitarbeiter in den Verbesserungsprozess wird nicht nur die Produktivität gesteigert, sondern auch die Motivation und das Engagement der Belegschaft gefördert. Diese kollektive Anstrengung führt zu einer dynamischen, lernenden Organisation, die flexibel auf Veränderungen reagieren und kontinuierlich wachsen kann. Kaizen fördert auch eine offene Kommunikationskultur, in der Vorschläge und Ideen aus allen Ebenen des Unternehmens willkommen sind und aktiv gefördert werden. Letztlich führt diese Philosophie zu einer ständigen Weiterentwicklung des Unternehmens, die es ermöglicht, langfristig wettbewerbsfähig zu bleiben und auf Marktveränderungen proaktiv zu reagieren.
Vorteile durch den Einsatz von LEAN Management
Lean-Prinzipien helfen Unternehmen, ihre Prozesse zu verschlanken und Verschwendung in jeglicher Form zu eliminieren. Durch die konsequente Ausrichtung auf wertschöpfende Tätigkeiten wird die Effizienz erheblich gesteigert. Ressourcen wie Zeit, Material und Arbeitskraft werden gezielt und effektiv eingesetzt. Dies führt nicht nur zu einer höheren Produktivität, sondern auch zu einer besseren Auslastung der vorhandenen Kapazitäten.
Die Fokussierung auf kontinuierliche Verbesserung (Kaizen) führt zu einer ständigen Optimierung von Produkten und Prozessen. Fehler und Mängel werden frühzeitig erkannt und behoben, bevor sie größere Probleme verursachen. Durch die Einbindung aller Mitarbeiter in den Verbesserungsprozess wird eine hohe Qualitätskultur geschaffen, die sich in der Zuverlässigkeit und Langlebigkeit der Produkte widerspiegelt.
Lean-Prinzipien tragen maßgeblich zur Reduzierung der Betriebskosten bei. Durch die Vermeidung von Überproduktion, die Minimierung von Lagerbeständen und die effiziente Nutzung von Ressourcen können Unternehmen ihre Kosten erheblich senken. Gleichzeitig ermöglicht die Just-in-Time-Produktion eine bedarfsgerechte Beschaffung, die zusätzliche Einsparungen bringt.
In einer sich ständig wandelnden Marktumgebung ist die Fähigkeit zur schnellen Anpassung entscheidend. Lean-Methoden fördern eine flexible Produktionsweise, die es Unternehmen ermöglicht, rasch auf Veränderungen in der Nachfrage zu reagieren. Die Reduzierung von Durchlaufzeiten und die Optimierung von Prozessen machen es leichter, neue Produkte schneller auf den Markt zu bringen und Kundenwünsche zeitnah zu erfüllen.
Lean-Prinzipien betonen die Bedeutung der Einbindung aller Mitarbeiter in den Verbesserungsprozess. Jeder im Unternehmen, unabhängig von seiner Position, wird ermutigt, Ideen zur Optimierung beizutragen. Dies fördert nicht nur das Verantwortungsbewusstsein, sondern steigert auch die Motivation und Zufriedenheit der Mitarbeiter. Eine solche Kultur der Zusammenarbeit und Wertschätzung wirkt sich positiv auf das gesamte Arbeitsklima aus.
Durch die konsequente Reduzierung von Verschwendung und die effiziente Nutzung von Ressourcen tragen Lean-Prinzipien auch zur ökologischen Nachhaltigkeit bei. Weniger Materialverbrauch, reduzierte Energiekosten und eine optimierte Logistik verringern den ökologischen Fußabdruck eines Unternehmens. Gleichzeitig wird durch die kontinuierliche Verbesserung und die ständige Anpassungsfähigkeit die Grundlage für langfristigen wirtschaftlichen Erfolg gelegt.
Letztlich zielt Lean Production darauf ab, den Kunden in den Mittelpunkt zu stellen. Durch die Konzentration auf wertschöpfende Aktivitäten und die Verbesserung der Qualität können Unternehmen Produkte und Dienstleistungen anbieten, die den Erwartungen der Kunden nicht nur gerecht werden, sondern sie oft sogar übertreffen. Dies führt zu einer höheren Kundenzufriedenheit, die sich direkt in einer stärkeren Marktposition und gesteigerter Wettbewerbsfähigkeit niederschlägt.
LEAN Production Werkeugkasten
- Wertstromanalyse (Value Stream Mapping)
- 5S-Methode
- Materialversorgung
- Kaizen (kontinuierliche Verbesserung)
- Shopfloor Management
- Montageoptimierung
- SMED
Wertstromanalyse (Value Stream Mapping)
Die Wertstromanalyse ist ein fundamentales Werkzeug im Lean-Ansatz. Sie ermöglicht es, den gesamten Produktionsprozess von Anfang bis Ende zu visualisieren und Schwachstellen sowie nicht-wertschöpfende Aktivitäten zu identifizieren. Durch diese Analyse können Unternehmen Engpässe aufspüren, Durchlaufzeiten verkürzen und Verschwendung reduzieren. Hier gehts zu unserem Training Wertstromdesign
5S-Methode
Die 5S-Methode zielt darauf ab, den Arbeitsplatz zu organisieren und zu standardisieren. Sie umfasst die Schritte Sortieren, Systematisieren, Säubern, Standardisieren und Selbstdisziplin. Durch diese Methode wird ein sauberer, aufgeräumter Arbeitsplatz geschaffen, der die Produktivität steigert und die Sicherheit erhöht. Hier gehts zu unserem 5S-Training
Materialversorgung
Kanban ist ein visuelles Steuerungssystem, das den Materialfluss in der Produktion regelt. Es basiert auf visuellen Signalen wie Karten oder Tafeln, um den Bedarf an Materialien zu signalisieren. Dies trägt zur Reduzierung von Überproduktion und Lagerbeständen bei, während gleichzeitig Engpässe und Unterbrechungen minimiert werden.
Kaizen (kontinuierliche Verbesserung)
Kaizen ist der Grundsatz der kontinuierlichen Verbesserung. Es ermutigt Mitarbeiter dazu, ständig nach Möglichkeiten zur Prozessoptimierung zu suchen und diese umzusetzen. Durch kleine, inkrementelle Veränderungen können Unternehmen ihre Effizienz stetig steigern.
Shopfloor Management
Shopfloor Management ist ein entscheidender Ansatz für die Effizienzsteigerung in der Fertigung. Es bezieht sich auf die direkte Überwachung und Steuerung von Produktionsprozessen auf der Werksebene. Durch klare Kommunikation, regelmäßige Meetings und visuelle Managementmethoden werden Engpässe, Probleme und Verbesserungspotenziale erkannt. Dies ermöglicht eine schnelle Reaktion, um Produktionsabläufe zu optimieren und Verschwendung zu minimieren. Shopfloor Management fördert zudem die Einbindung der Mitarbeiter in den kontinuierlichen Verbesserungsprozess, was zu einer gesteigerten Motivation und Effektivität führt. Letztendlich stärkt dieser Ansatz die Wettbewerbsfähigkeit von Unternehmen in einem dynamischen Marktumfeld.
Montageoptimierung
Produktionsprozesse zu optimieren, Durchlaufzeiten zu verkürzen und Kosten zu senken. Diese Strategie zielt darauf ab, Montageabläufe effizienter und reibungsloser zu gestalten, um letztendlich die Gesamtproduktionsleistung zu steigern. Montage ist ein kritischer Schritt in der Fertigung, der erheblichen Einfluss auf die Produktionskosten, Qualität und Lieferzeiten hat. Die Optimierung dieses Prozesses trägt dazu bei, Engpässe zu minimieren, Produktionszeiten zu reduzieren und die Effizienz zu steigern, was letztendlich zu höherer Kundenzufriedenheit und Wettbewerbsfähigkeit führt.
SMED
SMED (Single-Minute Exchange of Die) ist eine Methode zur Reduzierung von Rüstzeiten mit dem Ziel, diese auf einstellige Minutenwerte zu senken. Dabei werden interne und externe Rüstvorgänge getrennt, um parallele Abläufe zu ermöglichen. Mit Schnellspannsystemen und optimierten Prozessen wird die Flexibilität und Effizienz gesteigert. SMED macht Produktionsprozesse schlanker und wirtschaftlicher – ein Gewinn für jedes Unternehmen. Hier gehts zu unserem SMED Training / Workshop