Fabrikplanung
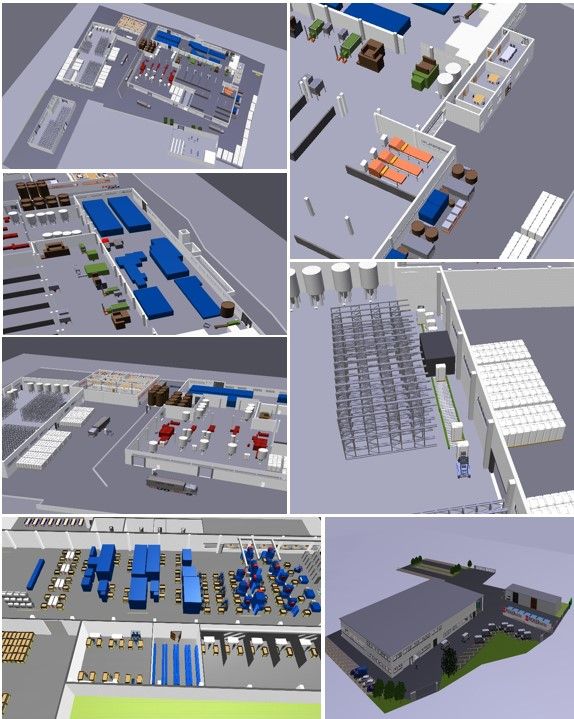
Die Planung, Optimierung und Realisierung von Produktions- und Logistikstandorten, egal ob auf der grünen Wiese oder im Bestand, stellt eine der herausforderndsten Aufgabenstellungen für Unternehmen dar.
Fehler, welche in der Planungs- und Realisierungsphase gemacht werden, können später nur mehr sehr schwierig oder gar nicht wieder behoben werden. Wir unterstützen Firmen von der Standortssuche bis zur vollständigen Realisierung von Werken.
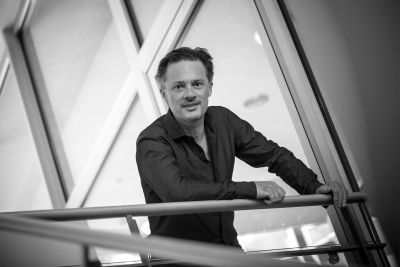
Walter Meitz
Ihr Kontakt für alle Rückfragen, Referenzen, Ablauf, etc.
Walter Meitz
+43 664 654 06 79
This email address is being protected from spambots. You need JavaScript enabled to view it.
Leistungsangebot
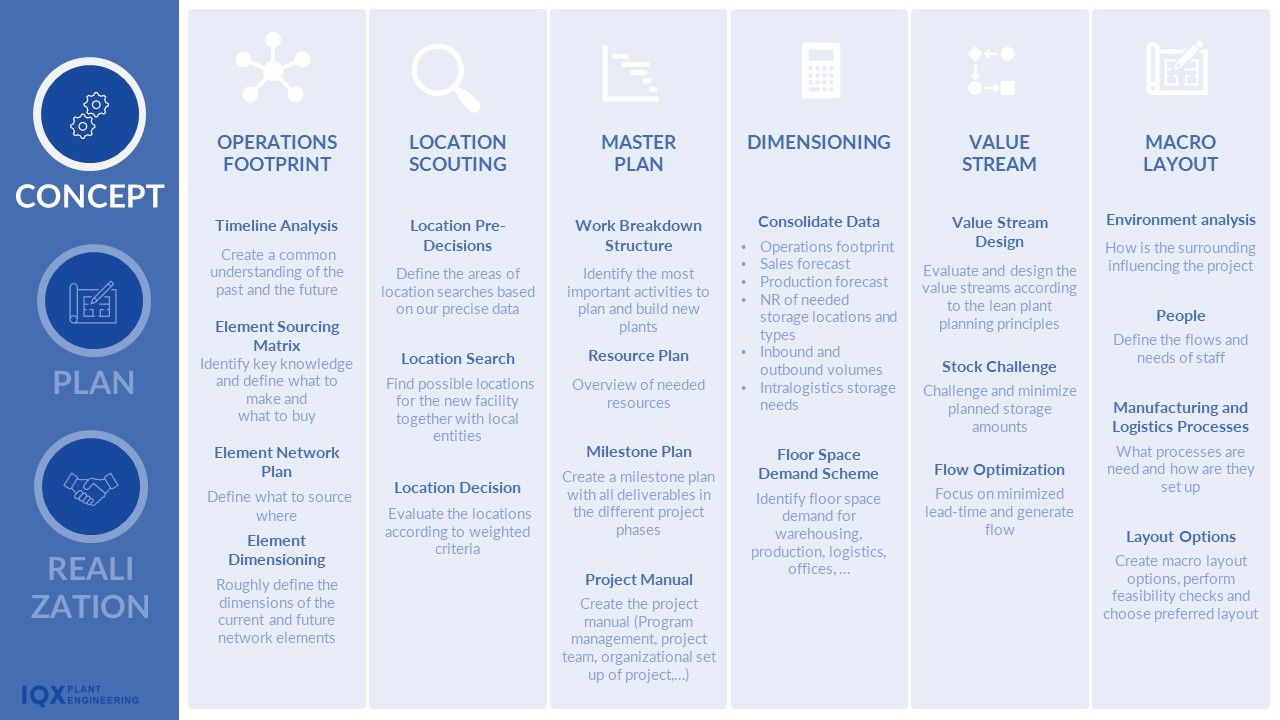
Der Begriff "Operations Footprint" bezieht sich auf die Gesamtheit der operativen Standorte und Aktivitäten eines Unternehmens. Dabei geht es nicht nur um die geografische Verteilung der Produktionsstätten, Lagerhäuser und Vertriebszentren, sondern auch um die strategische Ausrichtung der gesamten Wertschöpfungskette. Ein optimierter Operations Footprint stellt sicher, dass die betrieblichen Abläufe effizient, kostenbewusst und nachhaltig gestaltet sind, um die Unternehmensziele bestmöglich zu unterstützen.
Die Methode zur Analyse und Optimierung des Operations Footprint beginnt mit einer umfassenden Bestandsaufnahme. Hierbei werden alle Standorte und deren Funktionen detailliert erfasst und bewertet. Es geht darum, zu verstehen, wie jeder Standort zum Gesamterfolg des Unternehmens beiträgt und welche Kosten damit verbunden sind. Zudem werden externe Faktoren wie Marktanforderungen, Lieferkettenrisiken und geopolitische Einflüsse berücksichtigt.
Im nächsten Schritt erfolgt eine strategische Bewertung. Ziel ist es, herauszufinden, ob die aktuelle Struktur den künftigen Anforderungen gerecht wird. Dazu werden verschiedene Szenarien entwickelt, die unterschiedliche Markt- und Kostenentwicklungen simulieren. Diese Szenarien helfen, Chancen und Risiken aufzuzeigen und geben wertvolle Hinweise, wo eine Neuausrichtung notwendig sein könnte.
Die Umsetzung der Optimierungsmaßnahmen erfordert dann eine sorgfältige Planung und eine enge Abstimmung zwischen den beteiligten Abteilungen. Es geht darum, Prozesse zu harmonisieren, Synergien zu nutzen und möglicherweise Standorte neu zu positionieren oder gar zu konsolidieren. Wichtig ist hierbei, dass der Übergang reibungslos erfolgt und die Kontinuität im operativen Geschäft gewährleistet bleibt.
Ein optimierter Operations Footprint kann nicht nur Kosten senken, sondern auch die Flexibilität und Reaktionsfähigkeit des Unternehmens erhöhen. In einer sich ständig verändernden globalen Wirtschaft wird dies zunehmend zu einem entscheidenden Wettbewerbsvorteil. Unser Ziel ist es, gemeinsam mit Ihnen eine zukunftssichere Struktur zu schaffen, die Wachstum ermöglicht und gleichzeitig den Anforderungen von heute und morgen gerecht wird.
**Location Scouting für einen neuen Fabriksstandort** ist ein entscheidender Prozess in der strategischen Planung eines Unternehmens. Es handelt sich dabei um die systematische Suche und Bewertung potenzieller Standorte, die den spezifischen Anforderungen der geplanten Fabrik optimal entsprechen. Ziel ist es, einen Standort zu finden, der sowohl aus ökonomischer Sicht als auch in Bezug auf logistische, ökologische und soziale Faktoren den größtmöglichen Nutzen bietet.
### Vorgehensweise beim Location Scouting
1. **Definition der Standortkriterien:**
Der erste Schritt im Location Scouting besteht darin, klare Kriterien zu definieren, die der neue Standort erfüllen muss. Diese Kriterien können vielfältig sein und umfassen:
- **Kostenfaktoren:** Grundstückspreise, Steuern, Subventionen, Energiekosten und Lohnniveau.
- **Logistische Aspekte:** Nähe zu Zulieferern, Kunden, Verkehrsverbindungen (Straßen, Schienen, Häfen, Flughäfen) und Infrastruktur.
- **Arbeitsmarkt:** Verfügbarkeit qualifizierter Arbeitskräfte, Ausbildungsmöglichkeiten und Arbeitsmarktregulierungen.
- **Umweltfaktoren:** Umweltauflagen, Klimabedingungen, Energiequellen und Nachhaltigkeitspotenziale.
- **Soziale und kulturelle Faktoren:** Lebensqualität für Mitarbeiter, kulturelle Übereinstimmung und gesellschaftliche Akzeptanz.
2. **Erhebung und Analyse von Standortdaten:**
Sobald die Kriterien festgelegt sind, beginnt die Erhebung von Daten zu möglichen Standorten. Dies beinhaltet die Analyse von Makro- und Mikrofaktoren:
- **Makrofaktoren:** Wirtschaftliche Stabilität, politische Rahmenbedingungen, Handelsabkommen und rechtliche Aspekte.
- **Mikrofaktoren:** Verfügbarkeit von Infrastruktur, spezifische Standortkosten, Marktpotenziale und regionale Besonderheiten.
3. **Bewertung der potenziellen Standorte:**
Anhand der erhobenen Daten werden die Standorte bewertet und miteinander verglichen. Hier kommen oft Scoring-Modelle zum Einsatz, bei denen jeder Standort nach den definierten Kriterien Punkte erhält. Die Standorte mit den höchsten Gesamtpunkten werden dann für eine engere Prüfung in Betracht gezogen.
4. **Vor-Ort-Besichtigungen und Detailanalysen:**
Die vielversprechendsten Standorte werden anschließend vor Ort besichtigt. Dabei werden konkrete Gegebenheiten geprüft, wie die Beschaffenheit des Geländes, die Nähe zu Versorgungsnetzen und die tatsächliche Erreichbarkeit. Oft werden auch Gespräche mit lokalen Behörden und potenziellen Partnern geführt, um rechtliche und organisatorische Fragen zu klären.
5. **Risikoanalyse und Entscheidungsfindung:**
Vor der endgültigen Entscheidung wird eine umfassende Risikoanalyse durchgeführt. Dabei werden mögliche Risiken wie politische Instabilität, Naturkatastrophen, Lieferkettenrisiken oder soziale Konflikte bewertet. Auf Basis dieser Analyse trifft das Unternehmen dann die Entscheidung für den optimalen Standort.
6. **Verhandlungen und Vertragsabschluss:**
Nach der Standortauswahl folgen Verhandlungen mit den Grundstückseigentümern, lokalen Behörden und weiteren relevanten Akteuren. Es geht darum, die besten Konditionen für das Unternehmen zu sichern, einschließlich rechtlicher und steuerlicher Rahmenbedingungen, Investitionsanreize und anderer Vorteile.
7. **Planung der Implementierung:**
Ist der Standort festgelegt, beginnt die detaillierte Planung der Fabrik. Dies umfasst die architektonische Gestaltung, die Logistikplanung, die Einhaltung von Umweltauflagen und die Integration des Standorts in die bestehende Produktions- und Lieferkette.
Eine Work Breakdown Structure (WBS) ist ein Projektmanagement-Tool, das ein Projekt in kleinere, überschaubare Einheiten unterteilt. Es dient dazu, die gesamte Arbeit, die zur Erreichung eines Projektziels erforderlich ist, in einer hierarchischen Struktur darzustellen. Das Gesamtprojekt wird dabei in größere Komponenten zerlegt, die wiederum in detaillierte Arbeitspakete aufgespalten werden. Diese Pakete sind die kleinsten Einheiten, die geplant und verwaltet werden können, und ermöglichen eine klare Zuweisung von Aufgaben und Verantwortlichkeiten. Die WBS bietet so eine klare Übersicht, erleichtert die Planung und Kontrolle, und verbessert die Kommunikation im Projektteam.
Ressourcenplanung umfasst die Ermittlung und Zuweisung der notwendigen Mittel wie Personal, Material, Zeit und Budget, um ein Projekt erfolgreich durchzuführen. Sie stellt sicher, dass die benötigten Ressourcen in der richtigen Menge, zur richtigen Zeit und am richtigen Ort verfügbar sind. Dies schließt auch die Berücksichtigung von Kapazitäten, Verfügbarkeiten und Kosten ein, um eine effiziente Nutzung zu gewährleisten und Engpässe oder Überlastungen zu vermeiden.
Ein Meilensteinplan ist ein Überblick über die wichtigen Etappen eines Projekts, die als zentrale Fortschrittspunkte definiert werden. Er dient dazu, den Projektfortschritt zu überwachen, indem er festgelegte Zeitpunkte markiert, an denen bestimmte Ergebnisse oder Teilziele erreicht sein müssen. Dadurch ermöglicht der Meilensteinplan eine klare Orientierung und hilft, den Verlauf des Projekts zu steuern und rechtzeitig auf Abweichungen zu reagieren.
Ein Projekthandbuch ist ein umfassendes Dokument, das alle wesentlichen Informationen und Richtlinien für die Planung, Durchführung und Steuerung eines Projekts zusammenführt. Es dient als zentrale Referenz für das gesamte Projektteam und stellt sicher, dass alle Beteiligten über die Ziele, Rollen und Verantwortlichkeiten, Zeitpläne, Ressourcen, Kommunikationswege und Entscheidungsprozesse informiert sind. Durch die klare Dokumentation von Vorgehensweisen, Standards und Abläufen sorgt das Projekthandbuch für eine einheitliche Arbeitsweise und hilft, Missverständnisse und Ineffizienzen während der Projektumsetzung zu vermeiden. Es ist ein lebendiges Dokument, das im Verlauf des Projekts aktualisiert wird, um Änderungen und neue Erkenntnisse zu berücksichtigen.
Ein **Shopfloor Demand Scheme** ist ein strategisches System, das in der Fertigungsindustrie eingesetzt wird, um die Material- und Produktionsanforderungen direkt auf der Werkshalle, dem sogenannten Shopfloor, präzise zu steuern und zu synchronisieren. Ziel dieses Schemas ist es, die Materialversorgung und Produktionsabläufe optimal an den tatsächlichen Bedarf anzupassen, um eine hohe Effizienz, minimale Lagerbestände und kurze Durchlaufzeiten zu erreichen.
Im Kern des Shopfloor Demand Schemes steht die Idee, dass Materialien und Teile genau dann zur Verfügung gestellt werden, wenn sie in der Produktion benötigt werden – nicht früher und nicht später. Dies wird häufig durch den Einsatz von Just-in-Time (JIT)-Prinzipien oder Kanban-Systemen erreicht, die sicherstellen, dass die Produktion kontinuierlich mit den benötigten Materialien versorgt wird, ohne dass überflüssige Bestände aufgebaut werden.
Das System funktioniert, indem es die tatsächlichen Bedarfe, die direkt auf dem Shopfloor entstehen, erfasst und unmittelbar in Produktionsaufträge oder Materialanforderungen umsetzt. Dies geschieht in Echtzeit, sodass die Produktion flexibel und schnell auf Veränderungen in der Nachfrage reagieren kann. Zum Beispiel, wenn eine bestimmte Produktionslinie eine höhere Stückzahl eines bestimmten Teils benötigt, wird dies sofort im System vermerkt, und der Materialfluss wird entsprechend angepasst, um diesen Bedarf zu decken.
Ein weiterer Vorteil eines Shopfloor Demand Schemes ist die Verbesserung der Transparenz und Kommunikation auf der Werkshalle. Da das System die Nachfrage genau und zeitnah abbildet, können Produktionsleiter und Mitarbeiter sofort sehen, welche Materialien und Ressourcen benötigt werden und wann sie bereitgestellt werden müssen. Dies reduziert die Notwendigkeit für manuelle Eingriffe und Planungsanpassungen, was wiederum die Fehlerquote senkt und die Effizienz steigert.
Insgesamt unterstützt ein Shopfloor Demand Scheme eine reibungslose und kontinuierliche Produktion, die eng mit der tatsächlichen Nachfrage synchronisiert ist. Es trägt dazu bei, Kosten zu senken, die Produktionsflexibilität zu erhöhen und die Lieferzeiten zu verkürzen, indem es sicherstellt, dass alle benötigten Materialien und Teile genau dann verfügbar sind, wenn sie benötigt werden. Dies macht es zu einem unverzichtbaren Werkzeug in der modernen Fertigung, insbesondere in Umgebungen, in denen hohe Effizienz und schnelle Reaktionsfähigkeit auf Marktveränderungen entscheidend sind.
**Wertstromdesign** (oder **Value Stream Mapping**) ist eine Methode im Lean Management, die dazu dient, die gesamten Prozesse innerhalb einer Wertschöpfungskette zu analysieren und zu optimieren. Das Ziel ist es, Verschwendung zu identifizieren, die Effizienz zu steigern und die Wertschöpfung für den Kunden zu maximieren.
Wertstromdesign betrachtet alle Schritte, die notwendig sind, um ein Produkt oder eine Dienstleistung vom Rohmaterial oder der Bestellung bis hin zum fertigen Produkt beim Kunden zu bringen. Es umfasst nicht nur die physischen Prozesse der Produktion, sondern auch die Informationsflüsse, die diese Prozesse steuern. Durch die detaillierte Visualisierung des gesamten Wertstroms können ineffiziente Prozesse, Engpässe, Überproduktion und andere Arten von Verschwendung aufgedeckt werden.
Ablauf des Wertstromdesigns
1. Vorbereitung und Zieldefinition
Zu Beginn wird der Zielzustand definiert, also was mit der Wertstromanalyse erreicht werden soll. Es wird festgelegt, welche Produkte oder Dienstleistungen analysiert werden sollen und wer an der Analyse beteiligt ist.
2. Erfassung des Ist-Zustands
Im ersten Schritt wird der aktuelle Wertstrom erfasst und visualisiert. Dazu wird der gesamte Prozess, vom Eingang der Rohmaterialien oder Informationen bis zur Auslieferung des fertigen Produkts, detailliert dargestellt. Dabei werden sowohl die physischen Prozesse (wie Materialfluss und Fertigungsschritte) als auch die Informationsflüsse (wie Bestellungen, Steuerungsprozesse) abgebildet.
3. Analyse des Ist-Zustands
Nachdem der Ist-Zustand erfasst ist, wird er analysiert, um nicht-wertschöpfende Aktivitäten zu identifizieren. Das Ziel ist es, Engpässe, Verzögerungen, unnötige Bewegungen, Überproduktion, Wartezeiten und andere Verschwendungen sichtbar zu machen.
4. Entwicklung des Soll-Zustands
Auf Basis der Analyse wird ein optimierter Soll-Zustand entwickelt. Dabei werden Prozesse neu gestaltet oder eliminiert, um den Wertstrom effizienter zu gestalten. Der Fokus liegt darauf, die Wertschöpfung zu maximieren und Verschwendung zu minimieren. Oft werden hierbei Lean-Prinzipien wie Just-in-Time, Kanban oder Pull-Systeme eingeführt.
5. Umsetzungsplanung
Nachdem der Soll-Zustand definiert ist, wird ein detaillierter Umsetzungsplan erstellt. Dieser Plan legt fest, welche Maßnahmen in welcher Reihenfolge umgesetzt werden sollen, wer dafür verantwortlich ist und welche Ressourcen benötigt werden.
6. Implementierung und Überwachung
Der neue Wertstrom wird implementiert, und die Veränderungen werden in die Praxis umgesetzt. Während der Umsetzung ist es wichtig, den Fortschritt kontinuierlich zu überwachen und sicherzustellen, dass die geplanten Verbesserungen auch tatsächlich die gewünschten Effekte erzielen.
7. Kontinuierliche Verbesserung
Wertstromdesign ist ein iterativer Prozess. Nach der Implementierung des neuen Wertstroms wird der Prozess regelmäßig überprüft, um weitere Verbesserungsmöglichkeiten zu identifizieren. Der Kreislauf aus Erfassung, Analyse und Verbesserung wird fortgesetzt, um die Wertschöpfung kontinuierlich zu optimieren.
Ein **Groblayout** einer neuen Fabrik wird im Rahmen der Fabrikplanung erstellt, um eine erste, umfassende Übersicht über die räumliche Anordnung der wichtigsten Bereiche und Prozesse innerhalb der Fabrik zu erhalten. Es dient als grundlegendes Planungsinstrument, um sicherzustellen, dass die grundlegenden Anforderungen an den Materialfluss, die Produktionsprozesse, die Logistik und die Infrastruktur optimal berücksichtigt werden.
Durch das Groblayout können frühzeitig potenzielle Probleme und Engpässe identifiziert werden, die später zu ineffizienten Abläufen oder zusätzlichen Kosten führen könnten. Es hilft dabei, die Standorte von Produktionslinien, Lagern, Verwaltungsbereichen und anderen wichtigen Einrichtungen so zu platzieren, dass der gesamte Produktionsprozess möglichst effizient abläuft.
Das Groblayout ist ein entscheidendes Planungswerkzeug, das es ermöglicht, alternative Layouts zu vergleichen, die besten Optionen auszuwählen und eine solide Grundlage für die detaillierte Ausarbeitung des endgültigen Fabriklayouts zu schaffen. Es trägt zur Risikominimierung bei und stellt sicher, dass alle wesentlichen Planungsaspekte frühzeitig berücksichtigt werden, bevor in die detaillierte Planung und den Bau übergegangen wird.
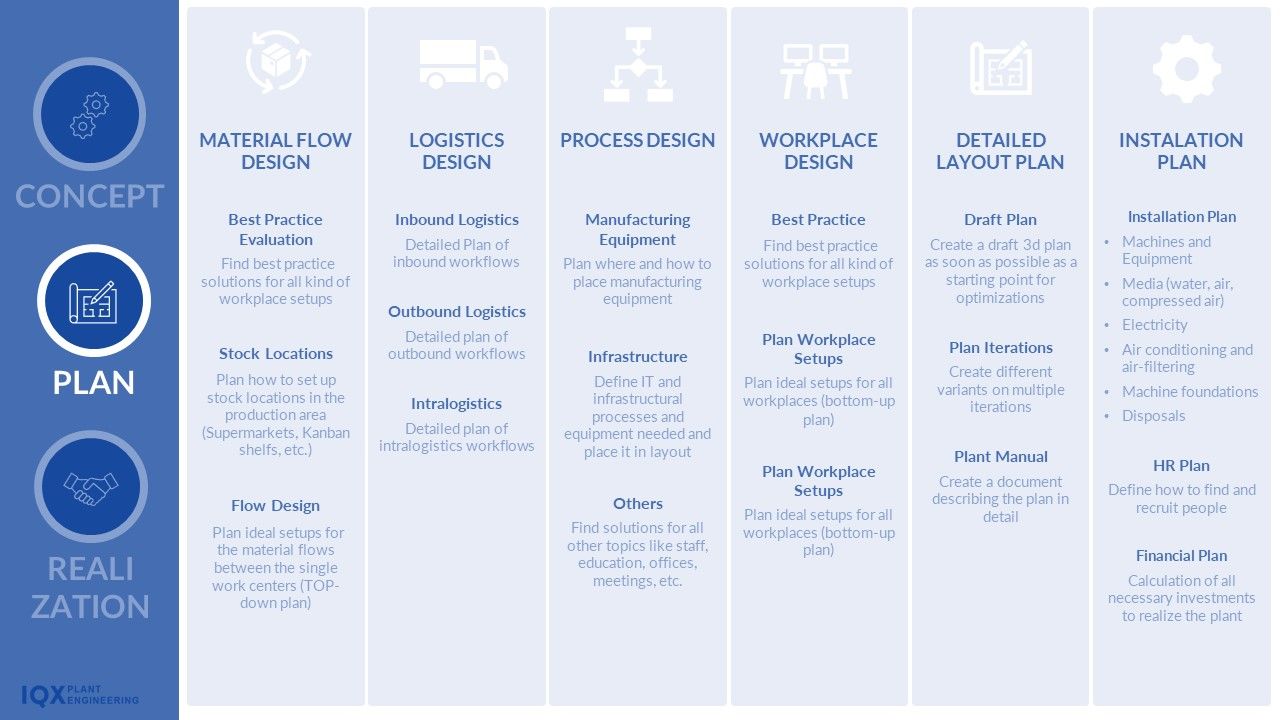
Materialflussdesign im Rahmen der Fabrikplanung bezieht sich auf die systematische Gestaltung und Optimierung des Flusses von Rohmaterialien, Halbfertigprodukten und fertigen Produkten innerhalb einer Fabrik. Ziel ist es, den Materialfluss so zu gestalten, dass die Produktionsprozesse effizient, kostengünstig und reibungslos ablaufen, während gleichzeitig unnötige Bewegungen, Wartezeiten und Lagerbestände minimiert werden.
Im Detail umfasst das Materialflussdesign die Planung der Wege und Transportmittel, die Materialien durch die verschiedenen Produktionsstufen führen. Es berücksichtigt die Platzierung von Maschinen, Lagerbereichen, Montageplätzen und Versandbereichen, um sicherzustellen, dass Materialien auf dem kürzesten und effizientesten Weg durch die Fabrik transportiert werden. Dabei wird auch der Einsatz von Fördertechnik, automatisierten Transportsystemen und Lagertechnologien berücksichtigt.
Ein gut durchdachtes Materialflussdesign trägt wesentlich zur Produktivität und Wettbewerbsfähigkeit einer Fabrik bei, da es dazu beiträgt, Produktionszeiten zu verkürzen, Kosten zu senken und die Flexibilität der Fertigungsprozesse zu erhöhen. Es stellt sicher, dass die gesamte Logistik innerhalb der Fabrik optimal auf die Produktionsanforderungen abgestimmt ist, was letztlich zu einer effizienteren und schlankeren Produktion führt.
**Logistikdesign** im Rahmen der Fabrikplanung bezieht sich auf die strategische Gestaltung und Optimierung der gesamten logistischen Prozesse innerhalb und außerhalb der Fabrik. Es umfasst die Planung und Koordination aller Aktivitäten, die mit dem Transport, der Lagerung, der Handhabung und der Verteilung von Materialien, Komponenten und Fertigprodukten verbunden sind.
Das Logistikdesign zielt darauf ab, den Fluss von Waren und Informationen so effizient wie möglich zu gestalten, um Kosten zu minimieren, die Lieferzeiten zu verkürzen und die Verfügbarkeit der benötigten Materialien sicherzustellen. Es berücksichtigt verschiedene Aspekte wie die Standortwahl von Lagern, die Gestaltung von Lagersystemen, die Auswahl und Implementierung von Transport- und Handhabungstechnologien sowie die Integration von Lieferkettenmanagement.
Ein effektives Logistikdesign stellt sicher, dass alle logistischen Prozesse nahtlos ineinandergreifen und optimal auf die Produktionsprozesse abgestimmt sind. Dies trägt dazu bei, Engpässe zu vermeiden, die Flexibilität zu erhöhen und letztlich die gesamte Wertschöpfungskette effizienter und wettbewerbsfähiger zu gestalten. Es umfasst sowohl die innerbetriebliche Logistik (z. B. den Materialfluss innerhalb der Fabrik) als auch die externe Logistik (z. B. die Beschaffung von Rohmaterialien und die Distribution von Fertigprodukten).
**Prozessdesign** im Zusammenhang mit der Fabrikplanung bezieht sich auf die Entwicklung und Optimierung der Produktionsprozesse, die innerhalb der Fabrik ablaufen. Es umfasst die detaillierte Planung aller Arbeitsschritte, die notwendig sind, um Rohmaterialien in fertige Produkte zu verwandeln. Ziel des Prozessdesigns ist es, effiziente, kostengünstige und qualitativ hochwertige Produktionsabläufe zu schaffen, die den Anforderungen des Unternehmens und des Marktes gerecht werden.
Im Rahmen des Prozessdesigns werden verschiedene Aspekte berücksichtigt:
- **Ablaufplanung**: Hier wird festgelegt, in welcher Reihenfolge die einzelnen Produktionsschritte erfolgen und wie sie miteinander verknüpft sind, um einen reibungslosen und effizienten Produktionsfluss zu gewährleisten.
- **Technologieauswahl**: Es wird entschieden, welche Maschinen, Anlagen und Technologien verwendet werden, um die Produktionsschritte auszuführen. Dabei spielt die Auswahl der optimalen Technologie eine zentrale Rolle, um Qualität, Geschwindigkeit und Kosten zu optimieren.
- **Arbeitsplatzgestaltung**: Die Anordnung und Ausstattung der Arbeitsplätze wird so geplant, dass sie die Produktivität der Mitarbeiter maximiert und gleichzeitig ergonomische und sicherheitstechnische Anforderungen erfüllt.
- **Qualitätskontrolle**: Es werden Maßnahmen und Kontrollen integriert, um die Qualität der Produkte in jeder Phase des Produktionsprozesses sicherzustellen.
Das Prozessdesign ist eng mit dem Materialflussdesign und dem Logistikdesign verknüpft, da es sicherstellt, dass die Produktionsprozesse effizient in die Material- und Logistikstrukturen integriert sind. Ein gut durchdachtes Prozessdesign minimiert Verschwendung, reduziert Durchlaufzeiten und trägt zur Kostensenkung bei, indem es die Abläufe so gestaltet, dass sie optimal auf die vorhandenen Ressourcen und logistischen Gegebenheiten abgestimmt sind.
Insgesamt bildet das Prozessdesign das Rückgrat der Fabrikplanung, da es die Grundlage für die effektive und effiziente Herstellung von Produkten legt und die Gesamtleistung der Fabrik maßgeblich beeinflusst.
Arbeitsplatzdesign im Rahmen der Fabrikplanung bezieht sich auf die Gestaltung und Anordnung der Arbeitsplätze, um die Effizienz, Sicherheit und Ergonomie für die Mitarbeiter zu maximieren. Es ist ein integraler Bestandteil des Gesamtprozesses, da es die Schnittstelle zwischen den Produktionsprozessen, den verwendeten Technologien und den Menschen, die in der Fabrik arbeiten, darstellt.
Das Ziel des Arbeitsplatzdesigns ist es, Arbeitsplätze so zu gestalten, dass die Mitarbeiter ihre Aufgaben effektiv und ohne unnötige Belastungen oder Gefahren ausführen können. Dazu gehören folgende Überlegungen:
- Ergonomie: Sicherstellung, dass Arbeitsplätze so gestaltet sind, dass sie körperlich angenehm und gesundheitsfördernd für die Mitarbeiter sind, um Verletzungen und Ermüdung zu vermeiden. Dies beinhaltet die richtige Höhe von Arbeitsflächen, bequeme Zugänglichkeit von Werkzeugen und Materialien sowie die Minimierung von sich wiederholenden, belastenden Bewegungen.
- Effizienz: Arbeitsplätze werden so gestaltet, dass Materialien, Werkzeuge und Maschinen optimal angeordnet sind, um unnötige Wege und Bewegungen zu vermeiden. Dies fördert eine höhere Produktivität und reduziert die Zeit, die für die Ausführung einer Aufgabe benötigt wird.
- Sicherheit: Integration von Sicherheitsmaßnahmen in die Arbeitsplatzgestaltung, um das Risiko von Unfällen und Verletzungen zu minimieren. Dies kann durch die Platzierung von Schutzvorrichtungen, klaren Sicherheitsanweisungen und der Berücksichtigung von Fluchtwegen erreicht werden.
- Flexibilität: Arbeitsplätze können so gestaltet werden, dass sie an unterschiedliche Aufgaben und Produktionsanforderungen anpassbar sind. Dies ist besonders wichtig in modernen Fabriken, die schnell auf Änderungen in der Produktion reagieren müssen.
Das Arbeitsplatzdesign ist eng mit dem Prozessdesign verbunden, da es die physische Umsetzung der geplanten Produktionsabläufe darstellt. Ein gut gestalteter Arbeitsplatz ermöglicht es den Mitarbeitern, die Produktionsprozesse effizienter zu gestalten, was wiederum zu einer höheren Gesamtproduktivität und Qualität führt. In Kombination mit dem Materialfluss- und Logistikdesign trägt das Arbeitsplatzdesign dazu bei, dass die gesamte Fabrik optimal funktioniert und sowohl die Leistung als auch das Wohlbefinden der Mitarbeiter maximiert werden.
In der Detailplanungsphase einer Fabrikplanung werden die zuvor entwickelten Konzepte und Layouts konkretisiert und in detaillierte Pläne umgesetzt. Ziel dieser Phase ist es, alle Aspekte der Fabrik bis ins kleinste Detail zu planen, um sicherzustellen, dass der Bau und die Inbetriebnahme reibungslos verlaufen und die Fabrik optimal funktioniert.
Wesentliche Schritte in der Detailplanungsphase
1. Detaillierung des Fabriklayouts:
Das Groblayout, das in früheren Phasen entwickelt wurde, wird in ein detailliertes Layout überführt. Hierbei werden alle Produktionsbereiche, Lagerflächen, Verkehrswege, Versorgungsleitungen und Arbeitsplätze präzise geplant und in den endgültigen Plänen festgehalten.
2. Integration von 3D-Planung:
In der Detailplanungsphase wird zunehmend auf **3D-Planung** gesetzt, um eine noch genauere und realistischere Darstellung der Fabrik zu ermöglichen. Mit 3D-Software können sämtliche Bereiche der Fabrik virtuell modelliert werden. Dies ermöglicht eine umfassende Visualisierung der Anordnung von Maschinen, Anlagen und Arbeitsplätzen, was die Erkennung von potenziellen Problemen oder Engpässen erleichtert. Die 3D-Modelle bieten außerdem die Möglichkeit, komplexe Zusammenhänge zwischen den verschiedenen Systemen und Strukturen frühzeitig zu verstehen und zu optimieren.
3. Planung der technischen Infrastruktur:
Alle technischen Systeme, wie Energieversorgung, Wasser- und Abwassersysteme, Lüftung und Klimatisierung, sowie IT- und Kommunikationsnetze, werden detailliert geplant. Hierbei wird auch die Integration dieser Systeme in das 3D-Modell berücksichtigt, um sicherzustellen, dass alle Leitungen und Anschlüsse korrekt verlegt werden und keine Kollisionen mit anderen Bauteilen entstehen.
4. Spezifikation von Maschinen und Anlagen:
In dieser Phase werden die genauen Spezifikationen der Maschinen und Anlagen festgelegt. Dies umfasst die Auswahl der Ausrüstungen, die Bestimmung der genauen Aufstellungsorte, die Planung von Schnittstellen zu anderen Systemen und die Berücksichtigung von Wartungsanforderungen. Die 3D-Planung hilft hierbei, die Maschinen präzise im Layout zu platzieren und deren Zugänglichkeit und Bedienbarkeit zu gewährleisten.
5. Arbeitsplatzgestaltung und Ergonomie:
Die detaillierte Gestaltung der Arbeitsplätze erfolgt unter Berücksichtigung ergonomischer Prinzipien, um die Effizienz und Sicherheit der Mitarbeiter zu maximieren. Mit der 3D-Planung können Arbeitsplätze virtuell getestet werden, um sicherzustellen, dass sie ergonomisch optimal gestaltet sind und dass alle Werkzeuge und Materialien leicht erreichbar sind.
6. Simulation und Optimierung:
Eine weitere Anwendung der 3D-Planung in der Detailplanungsphase ist die Simulation von Materialflüssen, Produktionsprozessen und Bewegungsabläufen. Diese Simulationen ermöglichen es, die Effizienz der geplanten Abläufe zu überprüfen und mögliche Engpässe oder Ineffizienzen bereits vor dem Bau der Fabrik zu identifizieren und zu beheben.
7. Vorbereitung der Bauausführung:
Auf Grundlage der detaillierten Pläne wird die Bauausführung vorbereitet. Dies beinhaltet die Erstellung von Bauplänen, die Koordination mit Bauunternehmen und Zulieferern, sowie die Planung des Bauablaufs. Die 3D-Modelle dienen dabei auch als Kommunikationsmittel zwischen den Planern, Ingenieuren und Bauunternehmen, um sicherzustellen, dass alle Beteiligten eine einheitliche Vorstellung des Projekts haben.
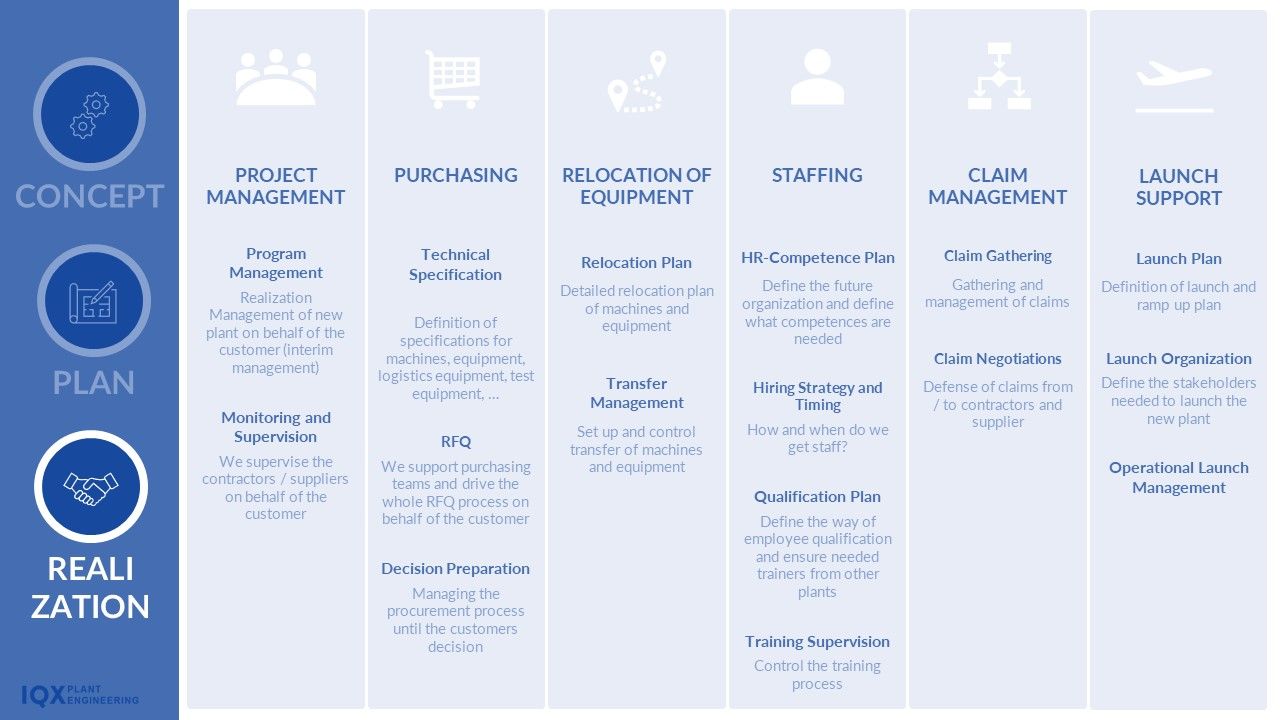
Bei der Umsetzung im Rahmen des Bauprojektmanagements wird der in der Detailplanungsphase entwickelte Plan in die Praxis überführt. Dieser Prozess umfasst mehrere zentrale Aktivitäten, die sicherstellen, dass der Bau der Fabrik effizient, termingerecht und innerhalb des Budgets realisiert wird.
Wesentliche Schritte im Bauprojektmanagement
1. Mobilisierung und Vorbereitung:
Zunächst werden die Baustelle eingerichtet und alle notwendigen Ressourcen, wie Materialien, Maschinen und Arbeitskräfte, bereitgestellt. Es wird sichergestellt, dass alle Genehmigungen vorliegen und die Baustelle den Sicherheitsvorschriften entspricht.
2. Überwachung und Steuerung der Bauarbeiten:
Während der Bauarbeiten überwacht das Bauprojektmanagement kontinuierlich den Fortschritt. Dazu gehören die Koordination der verschiedenen Gewerke, die Sicherstellung der Einhaltung des Bauzeitplans und die Überprüfung der Qualität der ausgeführten Arbeiten. Regelmäßige Baustellenbesprechungen mit allen Beteiligten sorgen dafür, dass alle auf dem gleichen Stand sind und etwaige Probleme schnell gelöst werden können.
3. Kosten- und Terminmanagement:
Ein zentraler Aspekt des Bauprojektmanagements ist die Überwachung der Kosten und Termine. Es wird sichergestellt, dass der Bau im Rahmen des festgelegten Budgets bleibt und dass die geplanten Meilensteine und Fertigstellungstermine eingehalten werden. Dazu gehört auch die Verwaltung von Änderungsaufträgen und die Anpassung des Plans, falls unvorhergesehene Ereignisse eintreten.
4. Qualitätskontrolle und Abnahme:
Um sicherzustellen, dass die Bauarbeiten den geforderten Standards entsprechen, werden regelmäßige Qualitätskontrollen durchgeführt. Dies umfasst sowohl die Prüfung der Bauausführung als auch die Einhaltung der technischen Spezifikationen. Am Ende jeder Bauphase wird eine Abnahme durchgeführt, bei der überprüft wird, ob alle Arbeiten ordnungsgemäß abgeschlossen wurden.
Beim Einkauf von Maschinen, Anlagen und technischem Equipment für eine neue Fabrik gibt es mehrere wichtige Aspekte zu beachten, um sicherzustellen, dass die Anschaffungen den Anforderungen der Produktion entsprechen und langfristig wirtschaftlich und effizient sind.
1. Anforderungsanalyse
Vor dem Einkauf ist eine genaue Analyse der Anforderungen notwendig. Dies beinhaltet die Definition der technischen Spezifikationen, die die Maschinen und Anlagen erfüllen müssen, um die Produktionsziele zu erreichen. Dabei sollten Aspekte wie Leistung, Kapazität, Flexibilität und Kompatibilität mit bestehenden Systemen berücksichtigt werden.
2. Qualität und Zuverlässigkeit
Die Qualität der Maschinen und Anlagen ist entscheidend für einen reibungslosen Betrieb. Es ist wichtig, auf die Zuverlässigkeit und Langlebigkeit der Produkte zu achten, um Ausfallzeiten und Wartungskosten zu minimieren. Die Auswahl sollte daher auf bewährte Hersteller und Technologien fallen, die für ihre Zuverlässigkeit bekannt sind.
3. Kosten und Budget
Neben den Anschaffungskosten müssen auch die langfristigen Betriebskosten berücksichtigt werden, einschließlich Wartung, Energieverbrauch und Ersatzteile. Eine umfassende Kosten-Nutzen-Analyse hilft, die wirtschaftlichste Option zu identifizieren. Auch die Möglichkeit von Finanzierung oder Leasing sollte geprüft werden, um die Investition zu optimieren.
4. Lieferzeiten und Verfügbarkeit
Die Lieferzeiten der Maschinen und Anlagen müssen mit dem Bauzeitplan der Fabrik abgestimmt werden. Verzögerungen bei der Lieferung können den gesamten Projektplan gefährden. Daher ist es wichtig, Lieferzeiten zu klären und gegebenenfalls Alternativen zu prüfen, um Engpässe zu vermeiden.
5. Service und Support
Ein zuverlässiger After-Sales-Service ist entscheidend für die langfristige Betriebssicherheit der Maschinen. Dazu gehört die Verfügbarkeit von technischem Support, schnelle Ersatzteilversorgung und die Möglichkeit regelmäßiger Wartungen. Es ist ratsam, die Serviceangebote der Hersteller genau zu prüfen und sicherzustellen, dass sie den Anforderungen entsprechen.
6. Technologische Kompatibilität
Die neuen Maschinen und Anlagen müssen nahtlos in das bestehende oder geplante Produktionsumfeld integriert werden können. Dies umfasst die Kompatibilität mit anderen technischen Systemen, Automatisierungslösungen und IT-Infrastrukturen. Eine mangelnde Integration kann zu erheblichen Effizienzverlusten führen.
7. Zertifizierungen und Vorschriften
Es ist sicherzustellen, dass die Maschinen und Anlagen allen relevanten gesetzlichen Vorschriften und Industriestandards entsprechen. Dies betrifft vor allem Sicherheitsstandards, Umweltauflagen und Energieeffizienzrichtlinien. Die Einhaltung dieser Vorschriften ist nicht nur aus rechtlichen Gründen wichtig, sondern trägt auch zur Nachhaltigkeit des Betriebs bei.
8. Schulung und Bedienbarkeit
Die Bedienung der neuen Maschinen sollte möglichst intuitiv und einfach sein, um die Einarbeitungszeit des Personals zu minimieren. Der Lieferant sollte Schulungen und Trainings anbieten, um sicherzustellen, dass das Personal die Maschinen sicher und effizient bedienen kann.
9. Zukunftssicherheit
Bei der Auswahl der Maschinen sollte auch die Zukunftssicherheit berücksichtigt werden. Dazu gehört die Möglichkeit, die Maschinen an zukünftige Anforderungen anzupassen oder zu erweitern. Investitionen in flexible und skalierbare Technologien können helfen, die Fabrik auf zukünftige Veränderungen vorzubereiten.
10. Vertragsgestaltung
Die vertraglichen Bedingungen für den Einkauf von Maschinen und Anlagen müssen sorgfältig ausgehandelt werden. Wichtige Punkte sind Garantiebedingungen, Haftung, Zahlungsmodalitäten und Lieferbedingungen. Es ist ratsam, rechtlichen Beistand hinzuzuziehen, um sicherzustellen, dass alle wichtigen Aspekte vertraglich abgesichert sind.
Der Einkauf von Maschinen, Anlagen und technischem Equipment ist ein komplexer Prozess, der sorgfältige Planung und Analyse erfordert. Durch die Berücksichtigung der genannten Aspekte kann sichergestellt werden, dass die getätigten Investitionen die Produktion optimal unterstützen und langfristig wirtschaftlich und effizient sind.
**Verlagerungsmanagement** beim Bau einer neuen Fabrik ist ein umfassender und komplexer Prozess, der weit über die reine physische Verlagerung von Maschinen und Anlagen hinausgeht. Es geht darum, die gesamte Produktionskapazität von einem bestehenden Standort auf einen neuen zu übertragen, ohne den laufenden Betrieb wesentlich zu stören und dabei die Effizienz der Produktion zu erhalten oder sogar zu steigern.
Der erste Schritt im Verlagerungsmanagement ist die detaillierte Planung. Hierbei werden Zeitpläne entwickelt, die den gesamten Prozess von der Demontage der Maschinen bis zur Wiederinbetriebnahme am neuen Standort abdecken. Es ist entscheidend, dass diese Zeitpläne realistisch sind und genügend Puffer für unvorhergesehene Ereignisse enthalten, um Produktionsausfälle zu vermeiden. Die Koordination der verschiedenen Aktivitäten – von der Logistik über die Neuinstallation bis hin zur Schulung der Mitarbeiter – muss in einem präzisen Ablaufplan festgehalten werden.
Ein weiterer wichtiger Aspekt ist die Ressourcenkoordination. Dazu gehört die Sicherstellung, dass alle benötigten Materialien, Maschinen und Ausrüstungen am neuen Standort rechtzeitig verfügbar sind und ordnungsgemäß installiert werden. Dies erfordert eine enge Zusammenarbeit mit Lieferanten, Transportdienstleistern und internen Teams. Die physische Verlagerung der Maschinen ist dabei besonders kritisch, da diese oft empfindlich und teuer sind. Deshalb müssen Transport, Sicherung und Wiederaufbau dieser Anlagen sorgfältig geplant und durchgeführt werden, um Schäden zu vermeiden.
Mitarbeitereinbindung spielt eine zentrale Rolle im Verlagerungsmanagement. Die Mitarbeiter müssen in den Verlagerungsprozess eingebunden und für den Umgang mit den Maschinen und Prozessen am neuen Standort geschult werden. Dies ist besonders wichtig, wenn neue Technologien oder veränderte Arbeitsabläufe eingeführt werden. Schulungen sollten frühzeitig und umfassend durchgeführt werden, um sicherzustellen, dass das Personal am neuen Standort nahtlos weiterarbeiten kann.
Die Testläufe am neuen Standort sind eine weitere kritische Phase des Verlagerungsmanagements. Vor der endgültigen Inbetriebnahme müssen alle Maschinen und Anlagen gründlich getestet werden, um sicherzustellen, dass sie einwandfrei funktionieren und die Produktion wie geplant aufgenommen werden kann. Diese Testläufe dienen auch dazu, letzte Anpassungen vorzunehmen und sicherzustellen, dass der Materialfluss und die Arbeitsabläufe optimiert sind.
Risikomanagement ist während des gesamten Verlagerungsprozesses von größter Bedeutung. Es ist wichtig, potenzielle Risiken wie Produktionsunterbrechungen, Verzögerungen, Transportschäden oder Probleme mit der Wiederinbetriebnahme frühzeitig zu identifizieren und entsprechende Gegenmaßnahmen zu planen. Dazu gehören beispielsweise Notfallpläne, alternative Lieferketten oder zusätzliche Ressourcen, die im Falle von Komplikationen schnell mobilisiert werden können.
Insgesamt ist Verlagerungsmanagement ein strategischer Prozess, der sorgfältige Planung, enge Koordination und präzise Ausführung erfordert. Durch eine erfolgreiche Umsetzung wird sichergestellt, dass die Produktionskapazitäten am neuen Standort effizient und ohne große Unterbrechungen übernommen werden können. Dies trägt dazu bei, dass die Fabrik von Anfang an optimal läuft und die gesteckten Ziele in Bezug auf Produktivität und Effizienz erreicht werden.
Beim Staffing, also der Personalbesetzung im Rahmen einer neuen Fabrik, geht es darum, die richtigen Mitarbeiter in ausreichender Anzahl und mit den passenden Qualifikationen für die unterschiedlichen Positionen zu gewinnen und zu integrieren. Der Prozess beginnt mit einer genauen Bedarfsanalyse, bei der die erforderlichen Rollen und Fähigkeiten definiert werden. Dabei wird festgelegt, welche Positionen notwendig sind, welche spezifischen Kompetenzen die Mitarbeiter mitbringen müssen und wie viele Mitarbeiter in den verschiedenen Bereichen benötigt werden.
Anschließend folgt die Rekrutierungsphase, in der geeignete Kandidaten gesucht werden. Dies kann sowohl intern, durch die Versetzung oder Weiterqualifizierung bestehender Mitarbeiter, als auch extern, durch das Anwerben neuer Talente, erfolgen. Der Rekrutierungsprozess muss sicherstellen, dass die ausgewählten Kandidaten nicht nur die fachlichen Anforderungen erfüllen, sondern auch zur Unternehmenskultur passen.
Sobald die Mitarbeiter ausgewählt sind, beginnt die Phase der Einarbeitung und Schulung. Hier ist es wichtig, dass die neuen oder versetzten Mitarbeiter umfassend auf ihre Aufgaben vorbereitet werden. Dies beinhaltet Schulungen zu spezifischen Maschinen und Prozessen, aber auch Einweisungen in Sicherheitsrichtlinien und Qualitätsstandards. Die Einarbeitungsphase sollte gut strukturiert sein, um den Übergang in die neue Rolle zu erleichtern und die Produktivität von Anfang an sicherzustellen.
Während dieses gesamten Prozesses ist es entscheidend, eine offene Kommunikation und klare Erwartungen zu gewährleisten. Mitarbeiter sollten jederzeit wissen, was von ihnen erwartet wird, welche Entwicklungsmöglichkeiten sie haben und wie ihre Rolle zur Erreichung der Unternehmensziele beiträgt. Zudem müssen Aspekte wie Arbeitsbedingungen, Vergütung und mögliche Karrierewege frühzeitig und transparent besprochen werden, um eine hohe Mitarbeiterzufriedenheit und -bindung zu gewährleisten.
Im Rahmen des Staffings ist es auch wichtig, eine langfristige Perspektive einzunehmen. Das bedeutet, nicht nur den aktuellen Bedarf zu decken, sondern auch potenzielle zukünftige Anforderungen im Blick zu haben. Hierbei spielen Themen wie die Fortbildung von Mitarbeitern, die Schaffung von Nachwuchskräften und das Management von Wissenstransfer eine wesentliche Rolle.
Zusammengefasst ist Staffing ein komplexer Prozess, der sorgfältige Planung und Umsetzung erfordert, um sicherzustellen, dass die neue Fabrik mit den besten verfügbaren Talenten besetzt wird und diese effektiv in die Arbeitsabläufe integriert werden. Durch gezieltes Staffing wird die Basis für einen reibungslosen Produktionsstart und den langfristigen Erfolg der Fabrik gelegt.
Claim Management ist nicht nur im Bauprozess einer Fabrik, sondern auch beim Einkauf und der Installation von Maschinen und Anlagen von zentraler Bedeutung. In einem Projekt dieser Größenordnung können vielfältige Herausforderungen auftreten, die zu Abweichungen vom ursprünglichen Vertrag führen. Diese Abweichungen können zusätzliche Kosten, Verzögerungen oder technische Probleme mit sich bringen, die sowohl den Bau als auch die Inbetriebnahme der Fabrik betreffen.
Beim Bau einer Fabrik können unvorhergesehene Ereignisse wie Verzögerungen im Bauablauf, Änderungen der Bauvorschriften oder unerwartete Bodenverhältnisse auftreten. Diese können zusätzliche Arbeiten und Kosten erfordern, die nicht im ursprünglichen Vertrag vorgesehen waren. Ohne ein effektives Claim Management könnten solche Situationen zu Streitigkeiten zwischen den Bauherren, Auftragnehmern und Subunternehmern führen, was den gesamten Projektverlauf gefährden könnte.
Ähnlich verhält es sich beim Einkauf und der Installation von Maschinen und Anlagen. Hier können Probleme wie Lieferverzögerungen, Abweichungen von den vereinbarten Spezifikationen oder Schwierigkeiten bei der Installation auftreten. Diese können erhebliche Auswirkungen auf den Zeitplan und das Budget des Projekts haben. Durch Claim Management wird sichergestellt, dass alle vertraglichen Verpflichtungen erfüllt werden und dass bei Abweichungen angemessene Kompensationen oder Anpassungen verhandelt werden können.
Claim Management ist daher unerlässlich, um sicherzustellen, dass sowohl der Bauprozess als auch die Installation und Inbetriebnahme der technischen Ausrüstung reibungslos und im Rahmen des Budgets und Zeitplans verlaufen. Es hilft, mögliche Konflikte frühzeitig zu erkennen und zu lösen, bevor sie eskalieren, und trägt so zur erfolgreichen Fertigstellung des Projekts bei.
Anlaufmanagement ist entscheidend, um den reibungslosen Start einer neuen Fabrik oder einer neuen Produktionslinie zu gewährleisten. In dieser Phase geht es darum, sicherzustellen, dass alle Systeme, Maschinen, Prozesse und das Personal optimal auf den Produktionsbeginn vorbereitet sind. Ein ineffizienter Anlauf kann zu erheblichen Problemen führen, wie etwa Produktionsverzögerungen, Qualitätsmängeln oder unerwarteten Kosten, die den gesamten Erfolg der Fabrik beeinträchtigen können.
Ein gutes Anlaufmanagement ermöglicht es, potenzielle Probleme frühzeitig zu identifizieren und zu beheben, bevor sie den Betrieb stören. Es umfasst die Überprüfung und Feinabstimmung von Produktionsprozessen, die Schulung des Personals und die Durchführung von Testläufen, um sicherzustellen, dass die Produktionsziele von Anfang an erreicht werden. Darüber hinaus spielt es eine wichtige Rolle dabei, die Kommunikation und Koordination zwischen den verschiedenen Abteilungen und Beteiligten zu fördern, um sicherzustellen, dass alle auf dem gleichen Stand sind und gemeinsam auf den erfolgreichen Start hinarbeiten.
Durch effektives Anlaufmanagement werden die Risiken minimiert, die mit dem Start einer neuen Produktion verbunden sind. Es sorgt dafür, dass die Produktion schnell hochgefahren werden kann, die Qualität stabil bleibt und das Unternehmen seine Markteinführungsziele erreicht. In einer Zeit, in der Schnelligkeit und Effizienz entscheidende Wettbewerbsvorteile darstellen, ist ein reibungsloser Anlauf ein Schlüsselfaktor für den langfristigen Erfolg einer neuen Fabrik.
Projektbeispiele
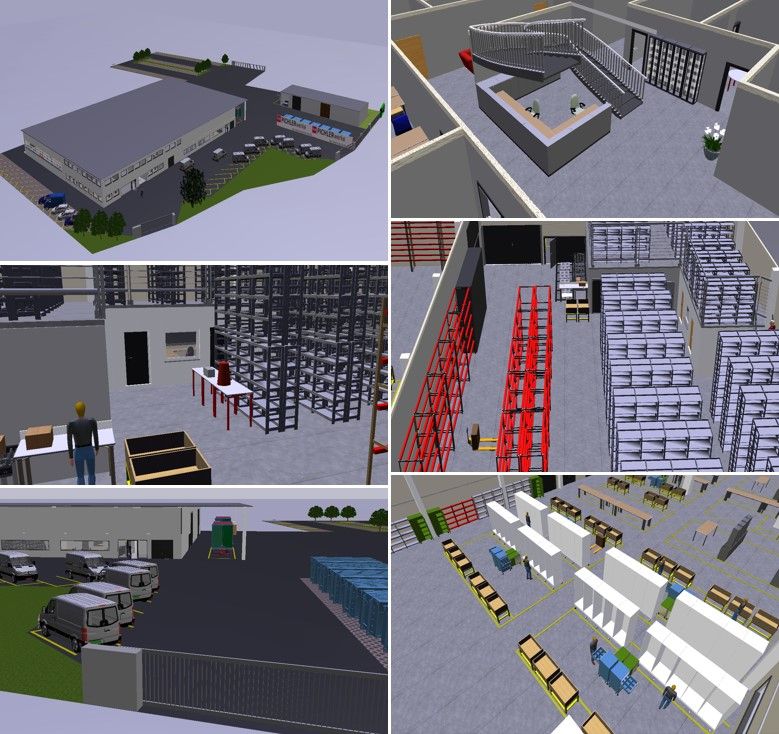
Werksneuplanung
Schaltschrankbau
Steiermark / Österreich
Detailplanung der Logistikprozesse
Detailplanung der Produktionsprozesse
Büroplanung
Montageoptimierung
Wirtschaftlichkeitsbetrachtungen
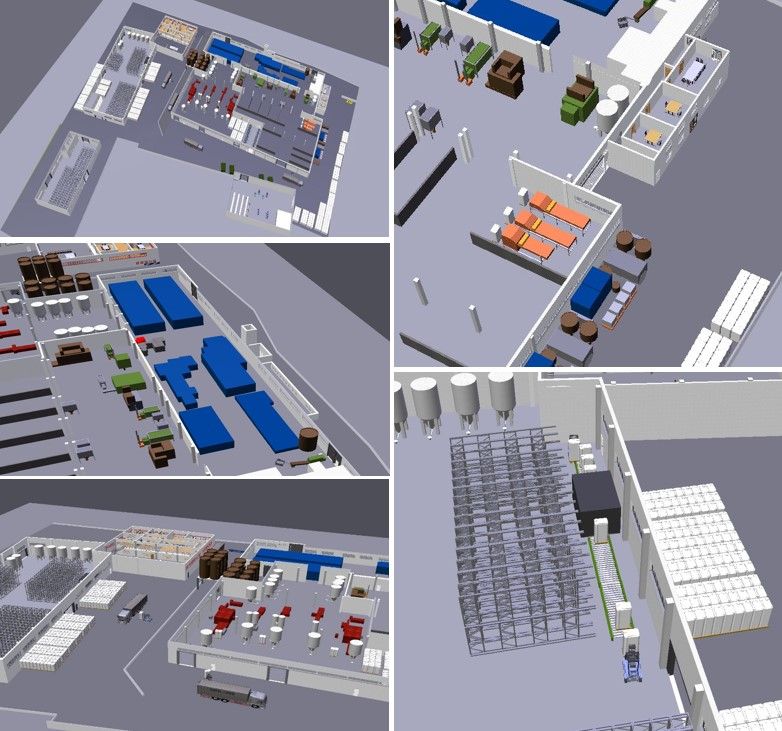
Werkserweiterungsplanung
Recyclingwerk
Venedig / Italien
Detailplanung der Logistikprozesse
Detailplanung der Produktionsprozesse
Büroplanung
Infrastrukturplanung
Umsetzungsplanung
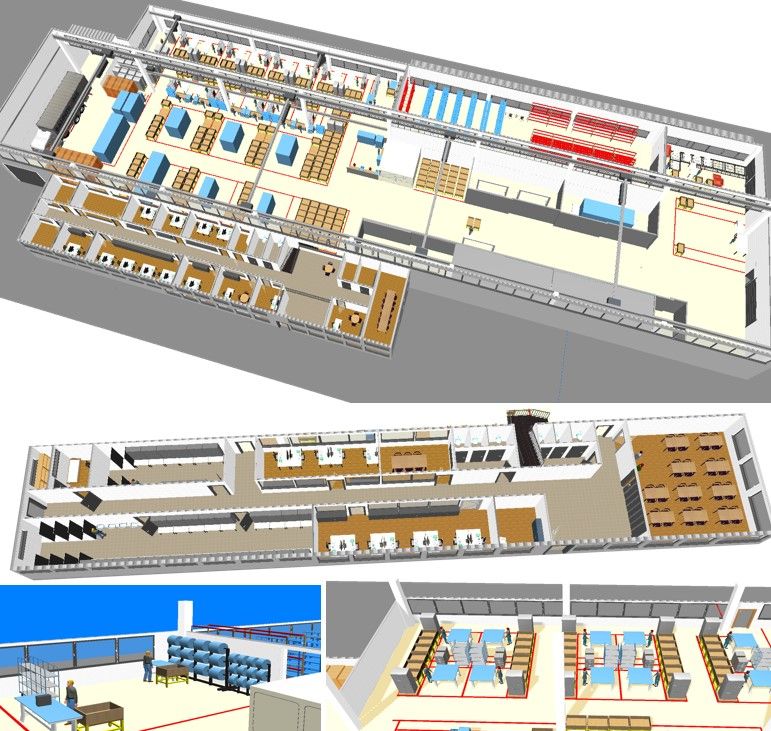
Werksneuplanung
Montagewerk
Satu Mare / Rumänien
Lagerplanung
Montageplanung
Produktionsprozessplanung
Büroplanung
Infrastrukturplanung

Werksneuplanung
Montagewerk
Steiermark / Österreich
Analyse der Logistikprozesse
Lagerkonzeptplanung
Montageplanung
Infrastrukturplanung
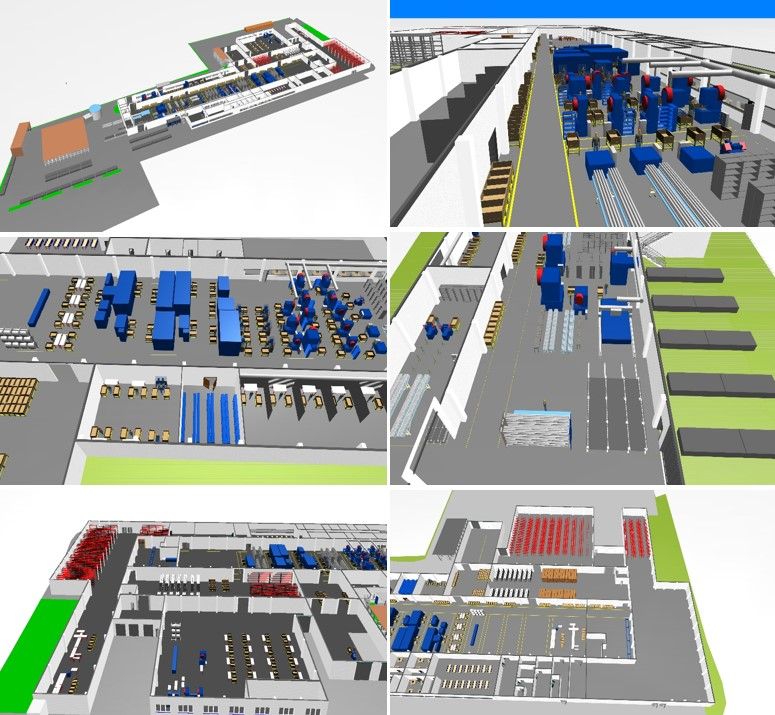
Werkstransfer
Komponentenwerk
Slowakei West
Analyse der Logistikprozesse
Lagerkonzeptplanung
Brownfieldplanung
Lagerplanung
Infrastrukturplanung
Transferbegleitung
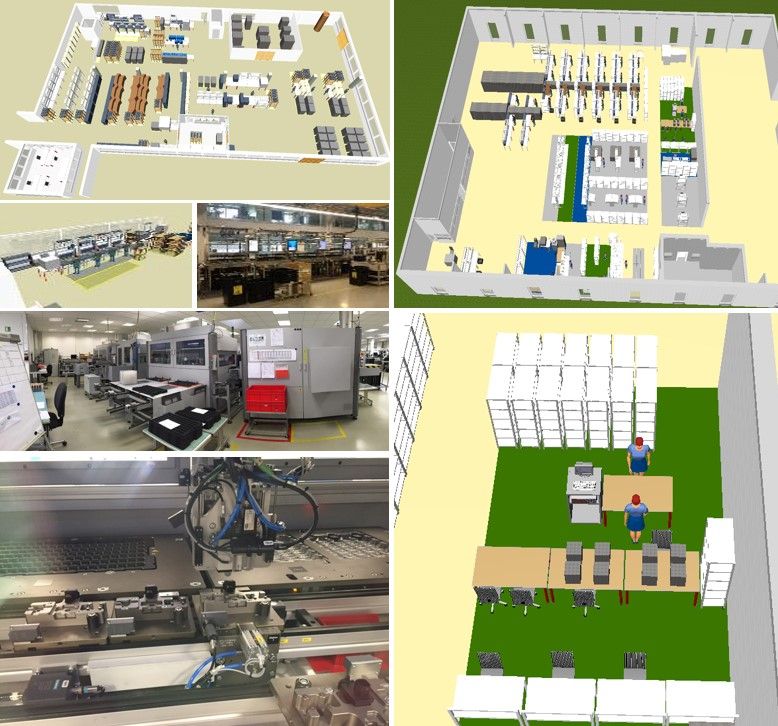
Werksentwicklungsplanung
Elektronikindustrie
Deutschland / Ungarn
Global Manufacturing Footprint
Detailplanung aller Logistik und Produktionsprozesse
Lageroptimierung
Montageoptimierung
Projektmanagement
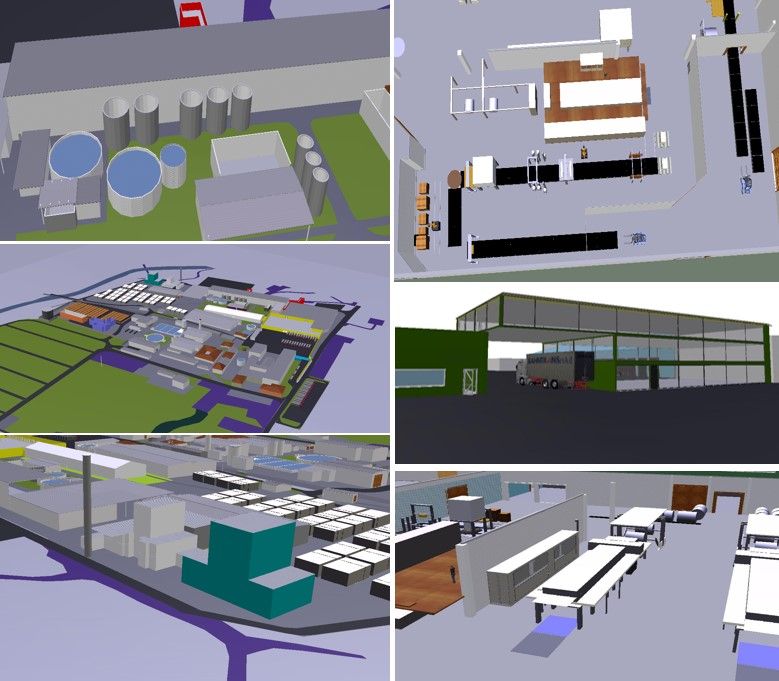